With today’s ever-increasing demand for quickly-produced manufactured goods, there is a need to create the gears utilized to run various equipment in numerous sizes and which can operate with the highest degree of accuracy. Read More…
Pioneer Broach Company is premier vendor of quality rotary broaching cutting tools. We specialize in custom spline, serration and hexalobular shaped rotary or wobble broaches, and also offer a complete line of standard hex and square rotary broach tools. Our new rotary broaching toolholder is designed for all modern CNC machines, mills and lathes.

Apex Broaching Systems is a worldwide supplier of standard broaching machines, special purpose broaching machines, fixturing, automation, and cutting tools. We have over 69 years of innovative engineering, skilled craftmanship, quality manufacturing, assembly, and customer satisfaction. All of our products are made here in the USA. Contact us today and tell us how we can meet your demands!

Diamond Broaching Service LLC showcases its value to its customers and the industry through quality customer service. The new team of Engineers and Machinists continue to provide the same high quality broaching services that our customers have depended on for over 70 years. With over 400 Broaching Tools in our inventory, we can respond quickly to provide the following shapes in just about all...

Since 1981, Universal Broaching has made a name as a dependable broaching job shop that offers quality products, impeccable service & competitive pricing for all broaching needs, no matter the size of the run. We offer horizontal internal broaching, vertical surface broaching, blind hole keyseating, broach sharpening, reconditioning & repair, and engineering & manufacturing of broaches & fixtures.

More Gear Hobbing Companies
Gear hobbing is the process of creating gear teeth through a “hob,” which is a rotating cutter. This process may be used for either high or low volume production of external cylindrical gears. The production rate of gear hobbing is relatively high compared to other gear-making techniques. The method can be used to make spur, helical, worm, sprocket, and spline gears, among other types of gears.
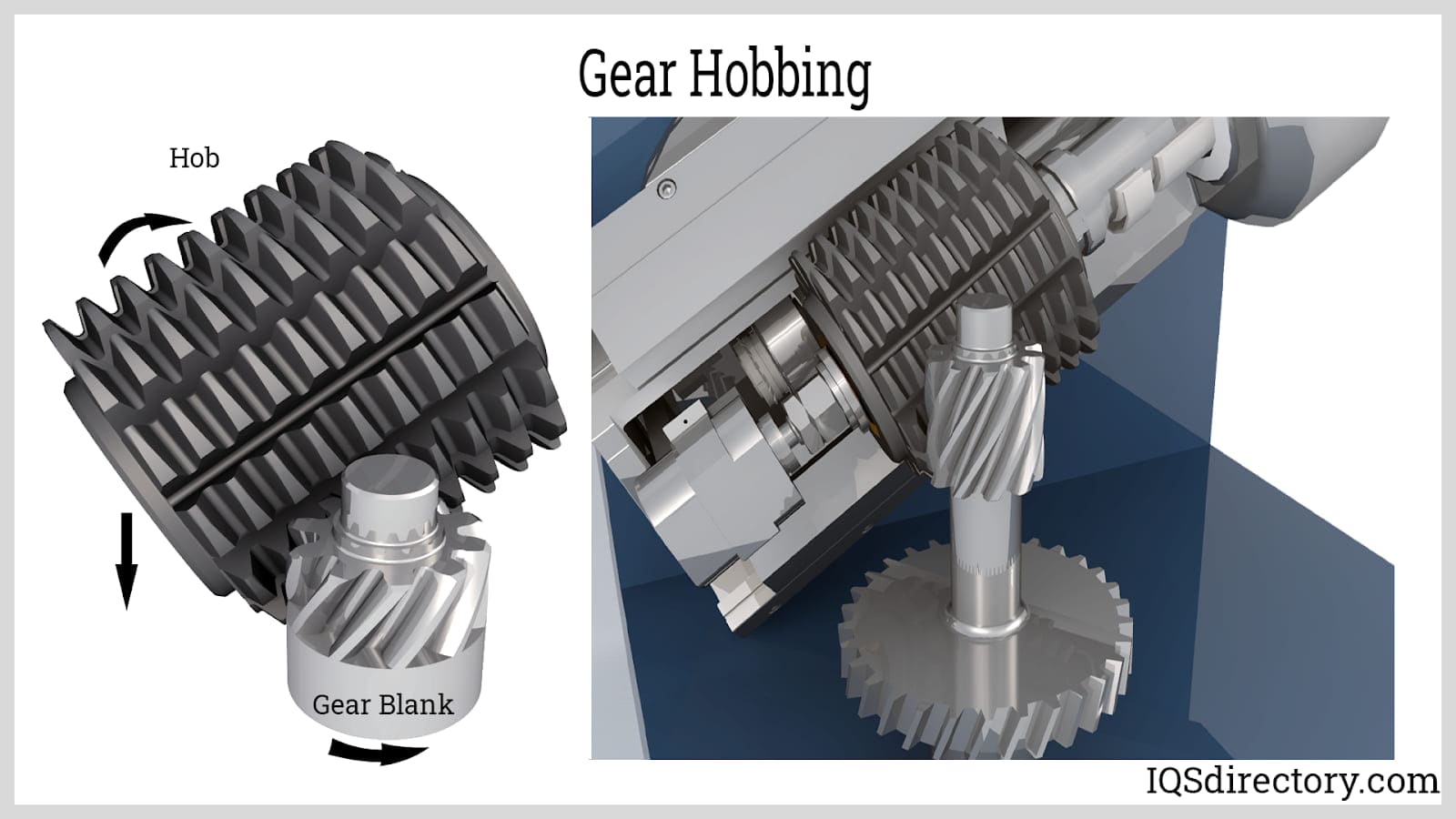
The Gear-Hobbing Process
Gear hobbing is a multi-step process. In the first step, a spinning cutter known as a hob is used to roll a gear blank. A multipoint cutting tool is then used. This tool resembles a worm gear with several straight flutes running parallel to its axis all around its circumference. These flutes are fashioned in such a way that they serve as cutting edges after being provided the correct angles. Next, the hob is fed to the gear blank while rotating at an appropriate rpm. The gear blank and gear hob's rpm are synced such that for every gear bob revolution, the gear blank rotates by a distance equivalent to one pitch of the gear that needs to be cut. This synchronization ensures that both the hob and the gear blank move consistently and steadily. In order for the hob's cutting blades to stay square with the gear blank during operation, it is tilted at a helix angle; the hob teeth then act like screw threads. A wide range of gears, including spur gears, helical gears, hearing-bone gears, splines, and gear sprockets, are made by gear hobbing.
Hob Positioning for Various Gears
After simultaneously spinning the gear blank and the cutter, known as a hob, with a fixed gearing ratio between the two, gears are cut. The gear blank is fed into the rotating hob until the necessary depth is obtained. Until all of the teeth are formed, the hob is fed across the blank's face. The hob teeth in a hobbing spur gear are positioned parallel to the blank's axis of rotation. Conversely, the axis of the hob is placed over an angle to create the proper helix for helical teeth bobbing. Worm gears, meanwhile, are made with the hob's axis fixed at a proper angle to the blank gear.
Techniques Used in the Hobbing Process
- Conventional hobbing: in this technique, the direction of the “feed (the moving direction of the hob in relation to the face of the workpiece)” matches the direction of the cutting motion. This technique produces a better finish but creates more wear.
- Climb hobbing: this technique has the feed in a direction opposite to the cutting motion. This technique is employed as a means to extend the tool’s life.
Hobbing Gear Parameters
Indexing movement, feed rate, and the angle between the axis of the gear blank and the gear hobbing tool are three crucial variables that must be under control (gear hob).
Hobbing Process Types
According to the hob's feeding directions for cutting gears, the gear- hobbing operation is divided into many groupings including axial feed, radial feed, and tangential feed categories as discussed below.
Gear Hobbing Using Axial Feed
In this procedure, the gear hob is fed against the gear blank parallel to its axis and along the blank's face. Gears like spur and helical gears are made using this operation.

Gear Hobbing Using Radial Feed
With this technique, the axes of the hob and gear blanks are arranged to be parallel to one another. The rotating hob is fed against the gear blank in a radial direction or perpendicular to the axis of the gear blank. Worm wheels are created using this process when the hob is positioned at the whole depth of the tooth and fed axially forward to the face of the gear blank; the hob is fed tangentially.

Gear Hobbing Using Tangential Feed
The teeth of a worm wheel are also cut using this method. The hob is held horizontally in this situation, with its axis oriented at the axis of the blank.

Benefits of the Gear-Hobbing Process
- When compared to other gear generation techniques, gear hobbing is an economical procedure since it is a quick and continuous operation.
- Its shorter manufacturing cycles results in a higher output rate.
- This process helps to create a wide range of gears, including worms, helical gears, spur gears, splines, and sprockets.
- By employing a method known as necessary indexing, the gear-hobbing process is relatively straightforward and able to produce any number of teeth while maintaining the module's accuracy.
- Gear hobbing alone can produce a specific kind of gear known as a herringbone gear (a special gear with a herringbone, or repeating V, pattern).
- The gear-hobbing process can handle a wide range of batch sizes, ranging from tiny to huge volumes.
- The gear-hobbing process makes it possible to process multiple gear blanks placed on the same arbor at once.
- Since a hob is a multipoint cutting tool with several cutting teeth or edges in itself, there are fewer cutting edges operating at once and there is more time for any heat created during this manufacturing process (and which may negatively affect the parts created) to be dissipated.
Drawbacks of the Gear-Hobbing Process
- The process is generally used to create external gears and typically requires additional setup for producing internal gears. Additionally, the machine must have the ability to fit a particular head for this purpose.
- The process cannot create bevel gears.
- There are size limitations regarding the gears it can produce.
- Producing splines or sprockets will require additional time to set up the machine to properly function.
Choosing the Proper Gear Hobbing Company
To make sure you have the most productive outcome when purchasing Gear Hobbing from a Gear Hobbing Supplier, it is important to compare at least 4 Companies using our Gear Hobbing directory. Each Gear Hobbing Company has a business profile page that highlights their areas of experience and capabilities and a contact form to directly communicate with the manufacturer for more information or request a quote. Review each Gear Hobbing business website using our patented website previewer to get an idea of what each business specializes in, and then use our simple RFQ form to contact multiple Gear Hobbing companies with the same form.